Safety Equipment & Hazard Prevention
Safety solutions by the Warehouse Lifeguards for superior protection of people, property, product and profit.
The Warehouse Lifeguards are Qualified Material Handling System Experts Who Ensure Workplace and Warehouse Safety
With evolving technology, work environments, and workforce demands, employers grow more concerned with safety. And OSHA fines are rising for companies who lack safe work conditions.
Your best defense to avoid severe injury or loss is through prevention. Basic prevention starts with a safety plan, routine safety checks of equipment and work areas, as well as proper protective gear and equipment. But in order to solve unique, complex safety challenges, it requires a skilled team with the right knowledge and experience.
Count on the Warehouse Lifeguards for all your safety solutions and equipment.
Warehouse Lifeguards – the name says it all. We identify potential hazards, develop safety strategies, and provide affordable solutions that work. You can count on us to safeguard your system.
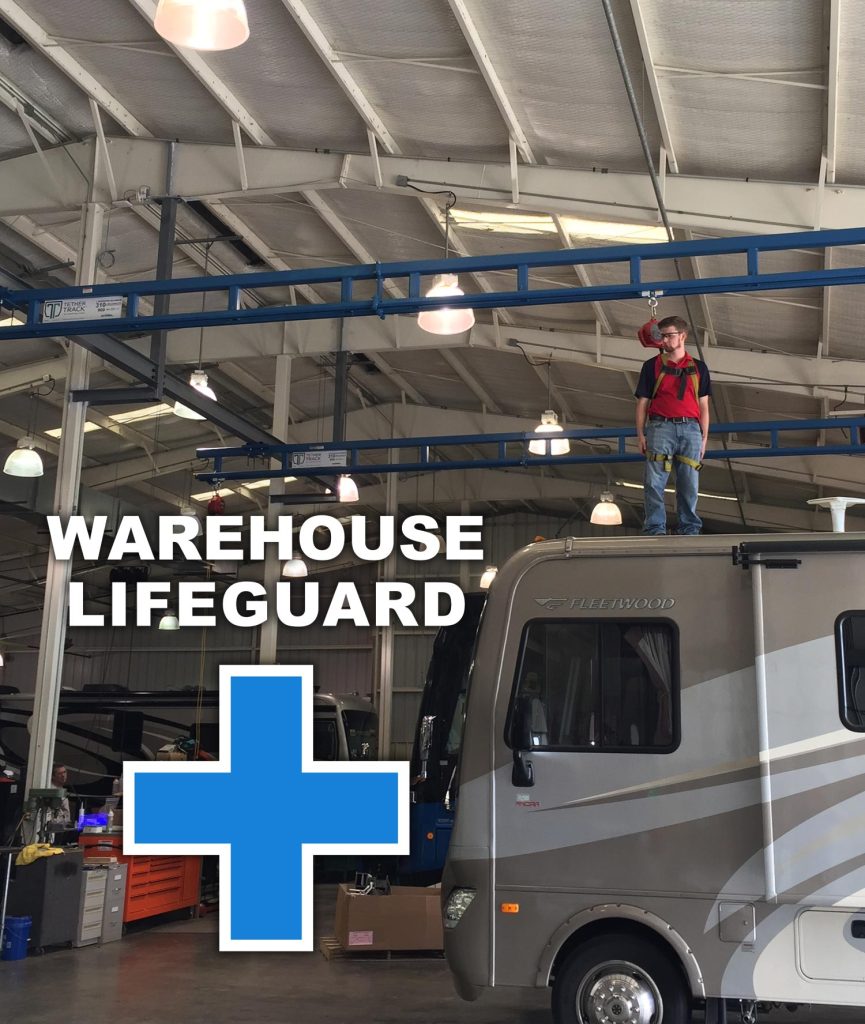
.
Schedule Your Consultation with Our Experts
W.W. Cannon’s Turnkey Service Solutions result in a strong return on your investment. Get in touch with one of our specialists today for a complimentary consultation. We’ll answer any questions you have and help you plan your next steps.