Our Client
Luxury Car Dealership in Dallas TX
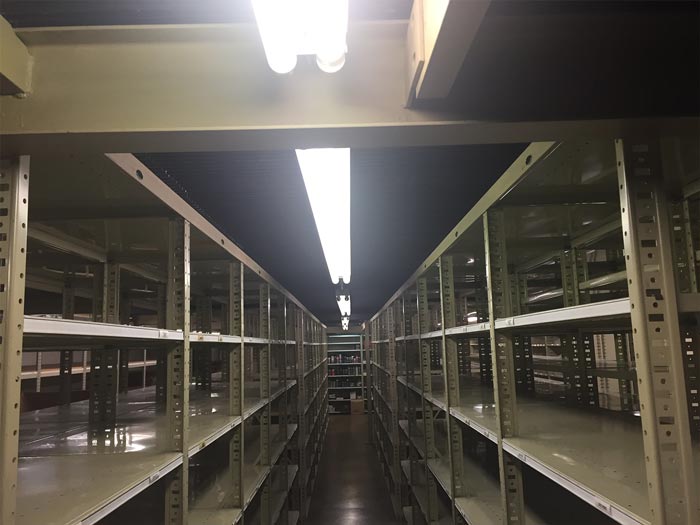
Our client has been offering the largest selection and service of luxury vehicles in the region since 1986. As a multi award winning retailer for quality, excellence and engagement, their focus on quality and expertise is second to none.
To accommodate for the expansion of their brand and new vehicles to show them in the best way possible, they needed to expand their facility.
The new space will include a performance showroom, expanded services center and an overall larger footprint for the selection of luxury vehicles.
The Challenge
Complete Location Breakdown, Storage & Reassembly
Expanding an active, thriving business is no small task. Closing its doors for a few weeks isn’t an option – too many people rely on our client’s team of highly skilled service technicians – not to mention their reputation for treating their car-buying clients to the luxury experience they deserve.
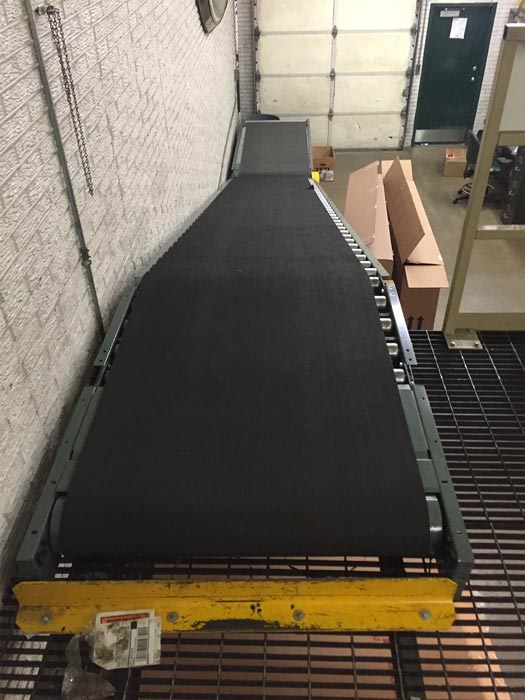
To get this job done, they needed the help of another highly skilled team; W.W. Cannon. For over seven decades, W.W. Cannon has been the name to trust for material handling solutions, industrial storage equipment, auto parts storage and service department equipment specialists.
The biggest challenge was the parts department. Everything needed to be moved out of the way; every part, big and small had to be dismantled and stored including their existing mezzanine. Automotive Specialist, Rode Chambers, lead the charge to prepare the Dallas auto dealership for its new space.
The Solution
W.W. Cannon Dismantles & Stores – Everything
“It felt like a ‘fire sale’, everything had to go,” said Chambers, “we got in there and packed every single thing up; all the parts bins, the modular drawers, the shelving – even the mezzanine.”
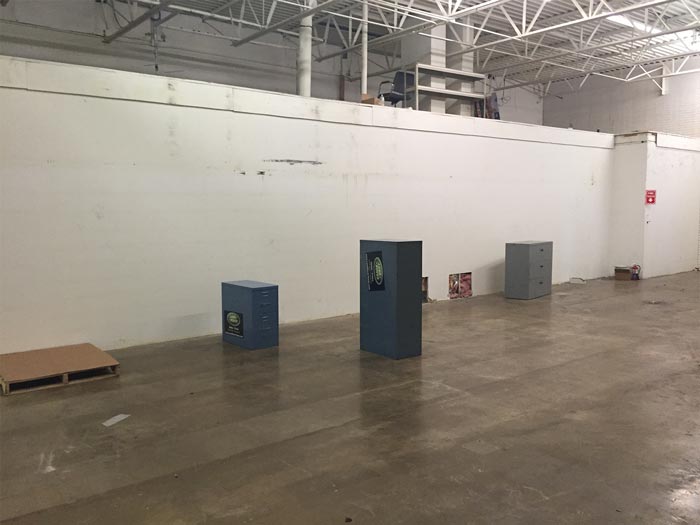
The installation crew tore down rows of auto parts shelving, workstations with modular drawers, service desks, the entire mezzanine work platform – everything in that parts and service center. W. W. Cannon’s skilled team of technicians also repaired the belt driven conveyor. All items were bundled for storage and placed into a 45-foot storage container.
“We’re managing the storage until their expansion is complete and they’re ready for us to come back in and set up their new parts department,” said Chambers.
The Results
All Packed & Ready to Go
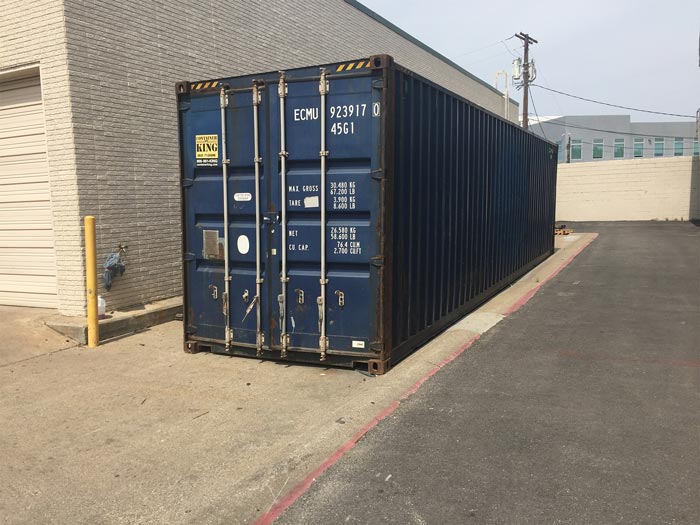
All of the equipment from our client’s parts department was packed up neatly and stored in a cargo container at a secured facility – awaiting the day of relocation and installation.
The auto service crew was happy with the dismantle, storage, relocation, and installation services they received.
Our turnkey services allowed for them to take care of business at hand – and not have to worry about contacting several different companies to take care of all the different phases of the move.
“They were impressed with the excellent job we did packing it up. They know we’re committed to seeing a project through – and done well,” said Chambers.
We offer complete material handling and industrial storage solutions, from design and project management, to install and follow-up.
To speak with us directly, call us at 800-442-3061. We’re ready to help you with the right solution for your needs.