Overhead Crane Runways
Convert Existing Warehouse Space into Manufacturing Space with Overhead Crane Runways
W.W. Cannon provides turnkey solutions for transforming existing retail or logistics spaces into light industrial manufacturing facilities. Our freestanding runway structures are designed, constructed, and installed to allow the integration of overhead crane systems into warehouse environments. Since these structures do not require attachment to the building’s framework, they can be easily removed and relocated as needed.
Runways in an overhead crane system consist of beams, columns, and rails that support the crane’s movement. The bridge or girder end trucks travel along rails secured to the top of the runway beams.
The support structure for these beams depends on the crane’s configuration. For top-running cranes, the beams are mounted to columns, while underhung cranes use beams supported by the building’s roof structure.
When installing a new crane in an existing building, it’s crucial to assess whether the building’s current columns can handle the crane’s load. If not, new columns must be added. These can be either tied-back columns, which connect to the building structure for added lateral support, or free-standing columns that are completely independent.
Overhead crane runways are available in both top-running and underhung configurations to suit different operational needs.
Overhead Crane Runways
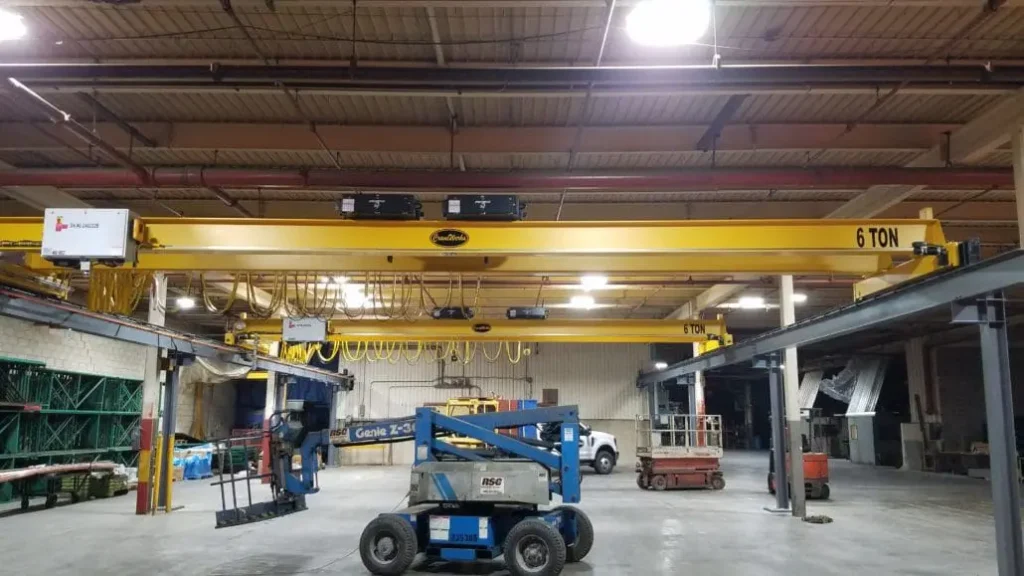
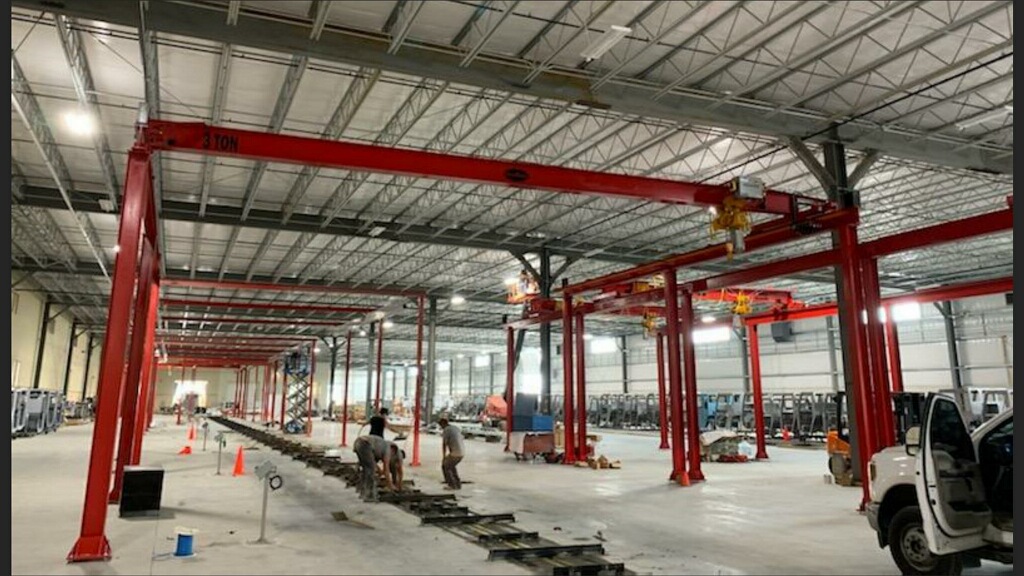
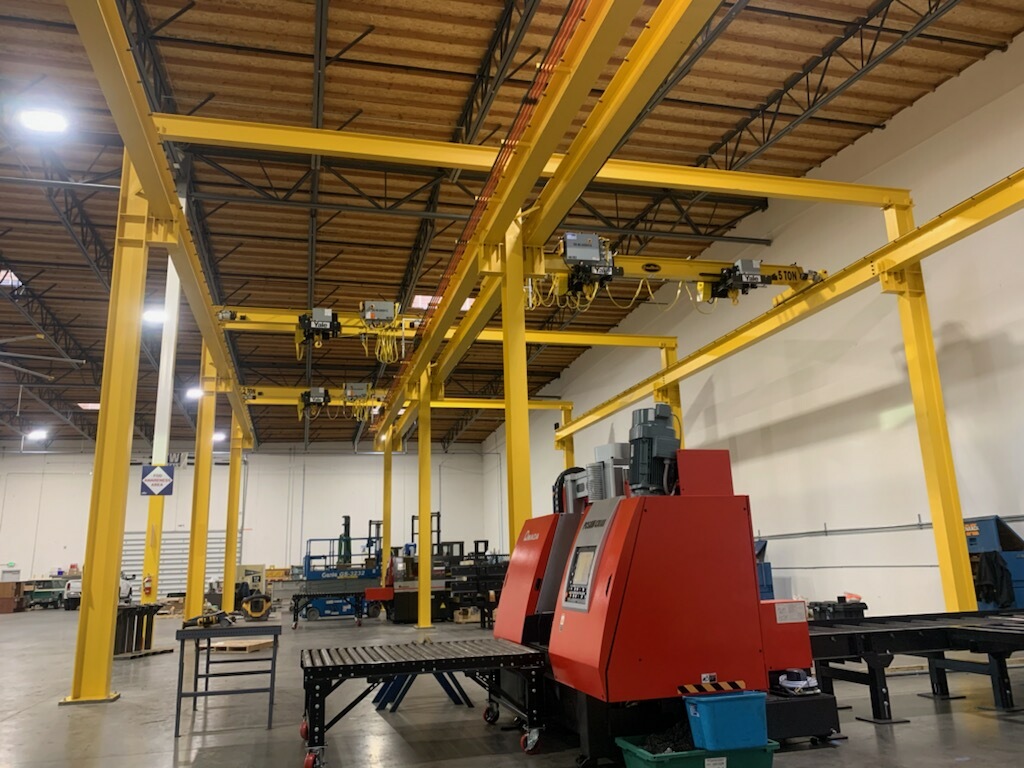
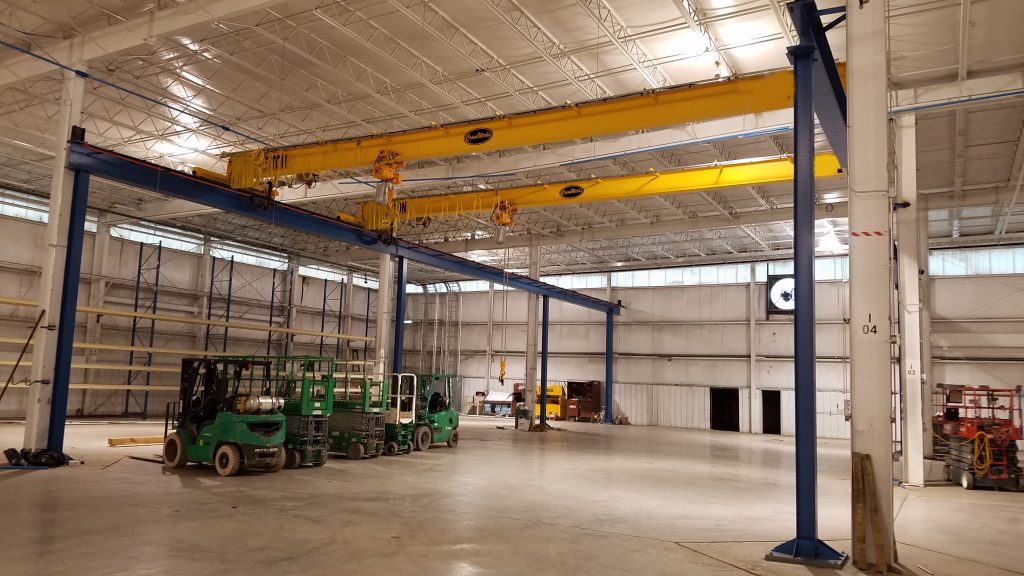
Freestanding Runway
Freestanding runways are ideal when maximum hook height is needed. These systems require at least 6 inches of concrete for floor mounting since they lack bracing. Without support headers across the top, the overhead bridge crane can operate at the very top of the structure, maximizing hook height. This design often provides an impressive additional hook height of 10 to 24 inches, making it a highly efficient solution in many applications.
Features include:
- Capacities typically range from 1 to 25-tons and higher
- Spans available up to 100-ft and longer
- Unlimited runway lengths
- Supports mount directly to a 6-inch concrete slab or reinforced concrete footers
- Hand gear, push type, electric and pneumatic cranes available
- Many configurations pre-engineered for quick delivery
- Ships complete with:
- Runway Electrification
- Hardware
- Assembly Manual
- Anchor Bolts*
- Complete AutoCAD drawings included
- Runway designs follow AISC specifications
- All systems are approved by a licensed PE
- Food grade and other noncorrosive equipment are available
Semi-Freestanding Runway
When a new or existing building has sufficient reserve capacity to withstand both longitudinal (along the length of the crane runways) and lateral (across the width of the runways) forces, columns and runways can be attached directly to the building. This approach reduces the amount of steel needed for an overhead crane system. These systems are ideal when minimizing floor obstructions and maximizing headroom (hook height) are priorities.
Engineering services are available to evaluate whether your building has the necessary strength to support cost-saving semi-freestanding crane runways.
Features include:
- Capacities vary from 1 to 50 ton
- Available in unlimited lengths
- Columns fasten directly into a 6-inch concrete floor or adequately sized foundation
- Push, motor driven, and hand geared bridge cranes available
- Custom engineered to meet your building specifications
- Ships complete with:
- Runway electrification
- Assembly manual
- Hardware
- Anchor bolts (if required)
- Comprehensive approval drawings supplied in Auto CAD format
- AISC specified runway systems
- Custom explosion proof and food grade systems are offered
- Licensed engineers review all system designs
Header-Braced Freestanding Runway
Header-braced runways are self-supporting systems designed for environments where minimizing floor obstructions is crucial. They are an excellent choice when the building’s lowest obstruction is high enough to allow installation while still providing sufficient headroom (hook height).
The key feature of top-running header-braced crane runways is a top-running bridge crane, with the bridge positioned on top of the runway. These systems eliminate the need for knee braces, maximizing valuable production space. Supported by freestanding columns, each pair of columns is connected by a header for added stability. Unlike some systems, stand-alone workstation bridge cranes do not rely on the building’s structure or support column integrity. Header-braced runways are particularly effective when building obstructions are positioned high enough to avoid limiting hook height.
Features include:
- Standard capacities from 1 to 25 ton and heavier
- Spans available up to 60 ft and wider
- Infinite runway lengths available
- Columns bolt directly to a 6-inch concrete slab or reinforced concrete foundations
- Electrical motor driven, hand geared, push type, and air powered overhead cranes available
- Quick deliveries available due to the pre-engineered designs
- Ships complete with:
- hardware
- assembly manual
- runway electrification
- anchor bolts (if required)
- Detailed approval drawings submitted in Auto CAD
- AISC specifications used throughout the design process
- Stainless steel systems for use in food industry or other corrosive applications
- Bolt together construction allows for easy installation, relocation, and expansion
- Professional engineers approve all system drawings
Knee-Braced Runway
Knee-braced runways are an excellent choice for applications requiring maximum hook height, provided the additional floor obstructions created by the knee braces are not an issue. This design is fully self-supporting and does not require attachment to the building or other structures.
Without support headers across the top, the overhead bridge crane operates at the very top of the structure, maximizing hook height. This design often provides an impressive additional hook height of 10 to 24 inches, making it a highly efficient solution in many setups. Features include:
- Capacities typically range from 1 to 25 tons and higher.
- Spans available up to 100 ft and longer.
- Unlimited runway lengths.
- Supports mount directly to a 6-inch concrete slab or reinforced concrete footers.
- Hand gear, push type, electric and pneumatic cranes are available.
- Many configurations are pre-engineered for quick delivery.
- Ships complete with:
- Runway Electrification
- Hardware
- Assembly Manual
- Anchor Bolts (when foundations are not required.)
- Complete AutoCAD drawings included.
- Runway designs follow AISC specifications.
- All systems are approved by a licensed PE.
- Food grade and other non-corrosive equipment is available
From design consultation to onsite project management and installation, W.W. Cannon can help you convert your existing warehouse space into manufacturing space with overhead crane runways. Did we mention that we have decades of experience navigating the permitting and code compliance process? Mismanagement of these issues can lead to project delays, emphasizing the importance of our expertise in handling them effectively. We also install and service everything we sell. Check out our overhead crane runways brochure, then contact us today and let one of our experts help you configure the right overhead crane runway for your application – on time and within your budget.
Preferred Suppliers
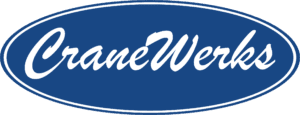
.
Schedule Your Consultation with Our Experts
W.W. Cannon’s Turnkey Service Solutions result in a strong return on your investment. Get in touch with one of our specialists today for a complimentary consultation. We’ll answer any questions you have and help you plan your next steps.