Drive-In/Drive-Through Racking
Drive-In and Drive-Through Racking Systems: A Cost Effective Solution to High-Density Storage
Drive-In and Drive-Through racking systems are static systems with rails running the depth of the rack for high-density storage of palletized goods. They are characterized by allowing forklifts to drive directly into the rack structure to access pallets. The drive-in rack depth reduces the need for aisles and dramatically increases cubic space utilization.
Drive-in racks utilize a Last-In, First-Out (LIFO) inventory management system, loading and retrieving items from the same side. This design provides cost-effective bulk storage while ensuring organized stock rotation. The supporting beam is positioned at the rear of the rack for stability.
Drive-through racks, on the other hand, follow a First-In, First-Out (FIFO) inventory management system. These racks allow loading from one end and retrieval from the opposite end, enabling seamless product flow. With a centrally located supporting beam, forklifts can drive straight through the structure for efficient access and handling.
Both systems are easy to install – simple support arms hold rails and can be attached to existing selective pallet rack or special structural designs.
If you have large volumes of like products, drive-in and drive-through rack is a perfect fit. Due to the Last-In, First-Out inventory method, drive-in rack provides limited selectivity. Drive-through racks offer a bit more selectivity since pallets can be accessed from either end of rack. Dense storage can create space for up to seven times more product than floor stacking and three times more than pallet rack because pallets are stored back-to-back, floor-to-ceiling.
These high-density racking systems are typically subject to more abuse than selective racks due to the way they are utilized, so rack integrity and strength are very important factors. The choice between drive-in and drive-through depends on the desired inventory management method (LIFO or FIFO) and the level of selectivity required.
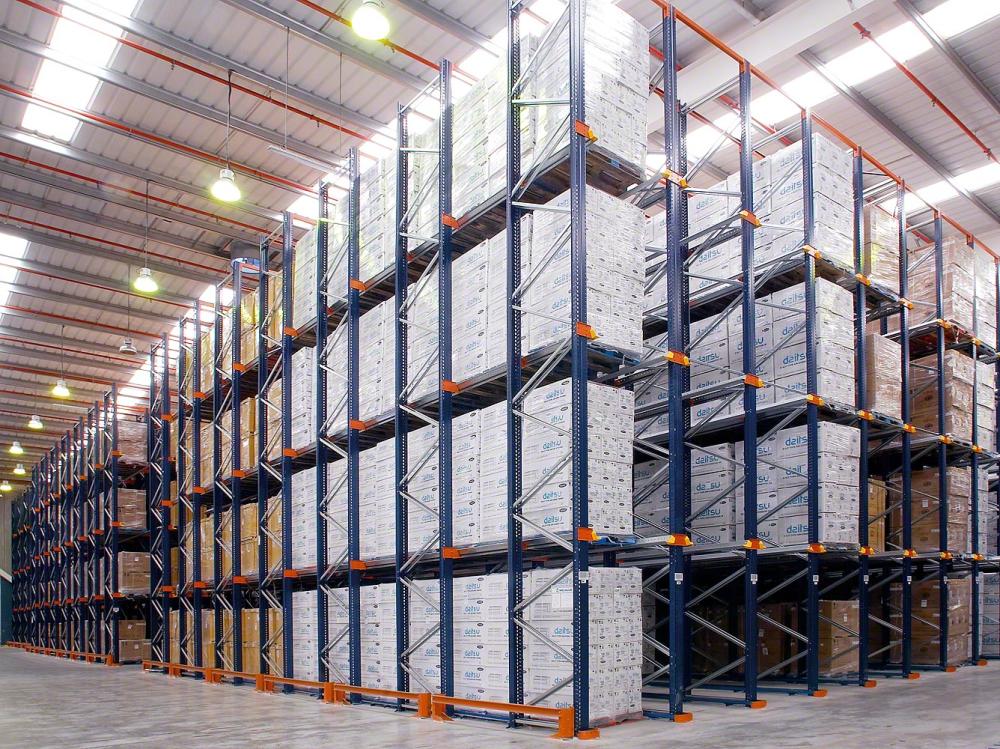
Common Applications
Cold Storage
Commonly used in cold storage facilities where maximizing storage density is critical.
Bulk Storage
Suitable for storing large quantities of homogeneous products where batch or date rotation is not a primary concern.
Limited Aisle Space
Ideal for facilities with limited aisle space as they eliminate the need for multiple aisles between racks.
Seasonal Inventory
Highly effective for businesses with seasonal inventory fluctuations that require high-density storage during peak seasons.
Cost-Efficient Storage
Ideal for maximizing warehouse space utilization since their dense storage method can create space for up to seven times more product than floor stacking and three times more than pallet rack since pallets are stored back-to-back and floor-to-ceiling.
Photo Gallery
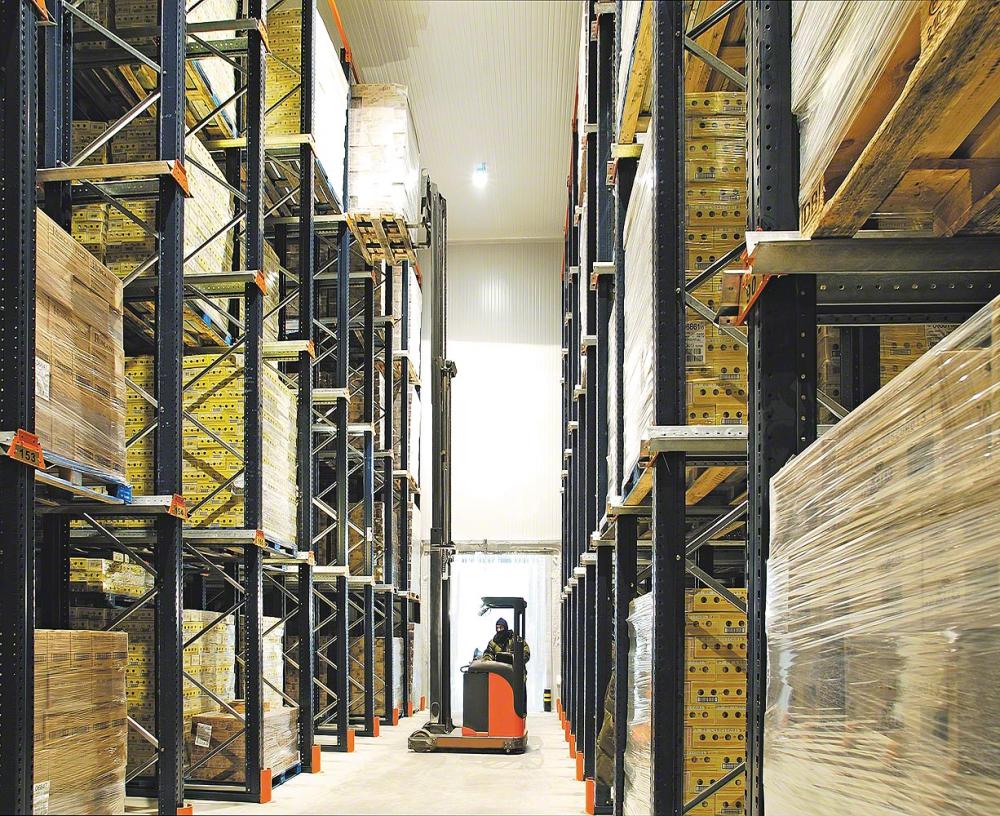
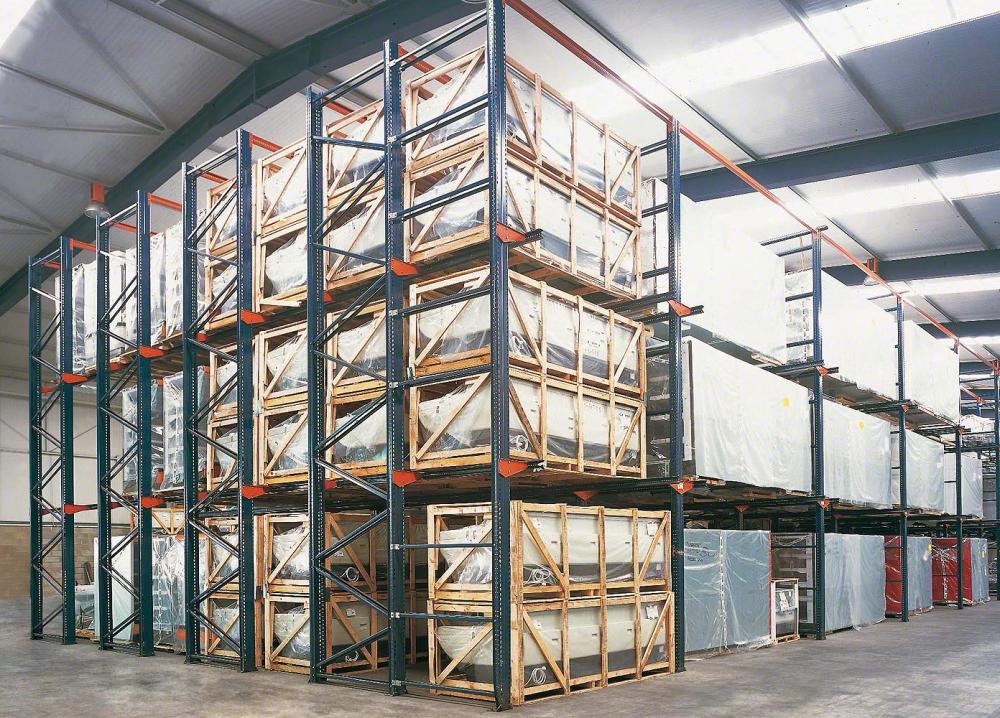
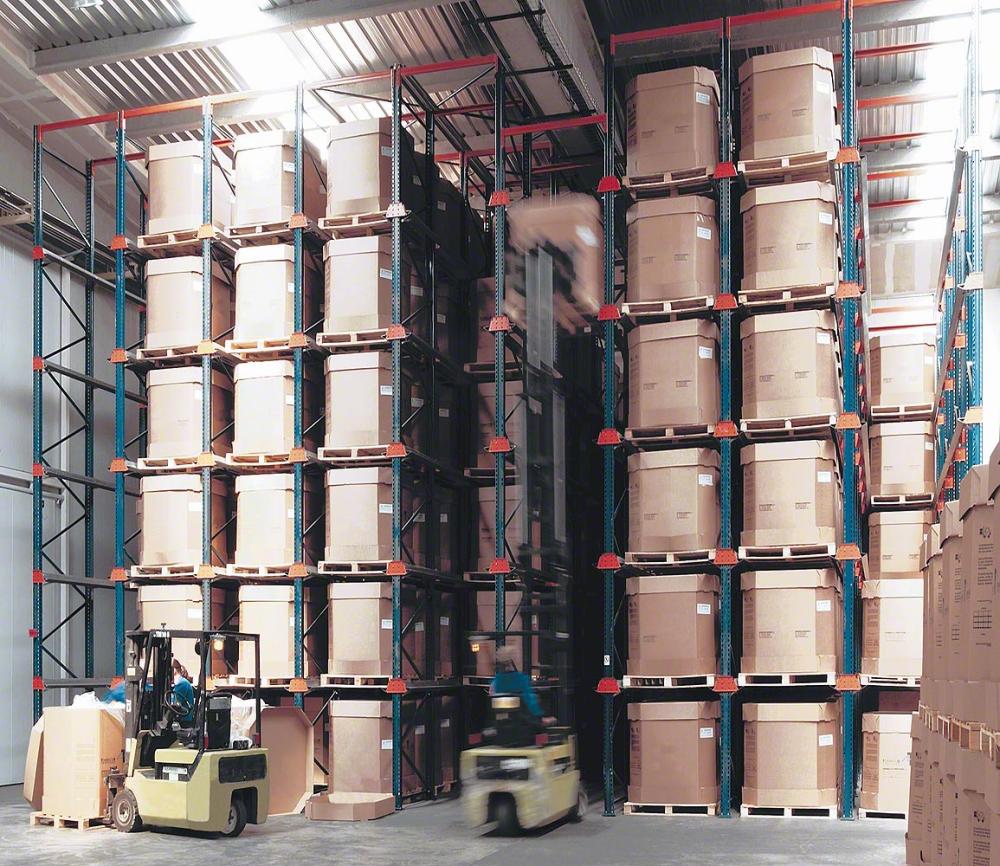
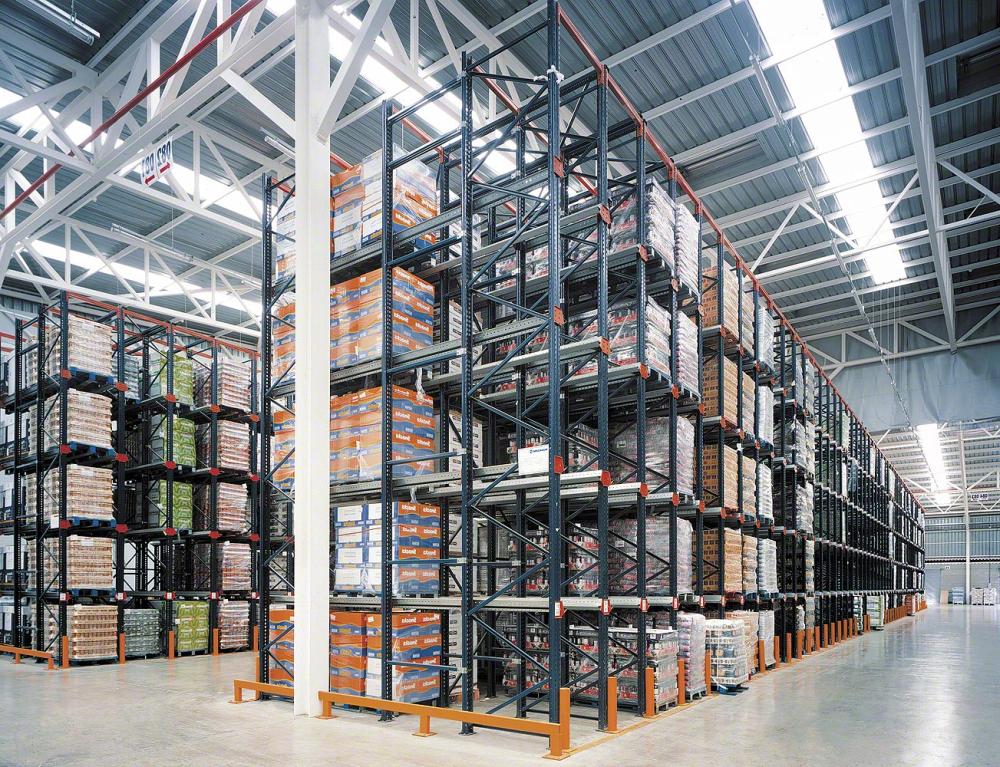
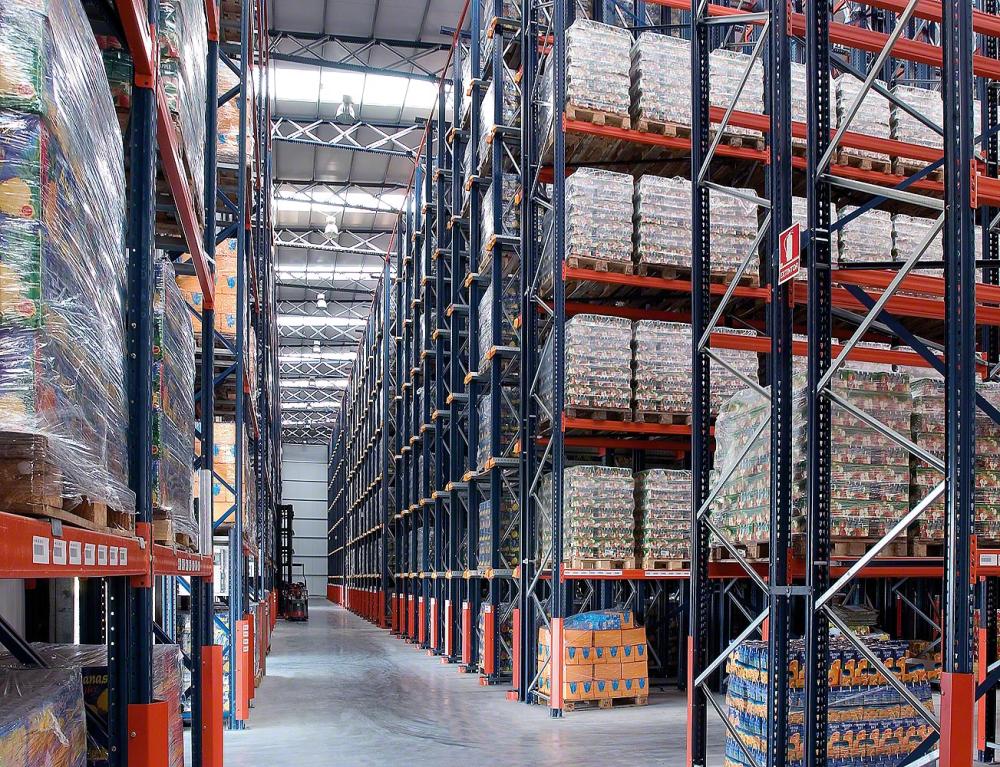
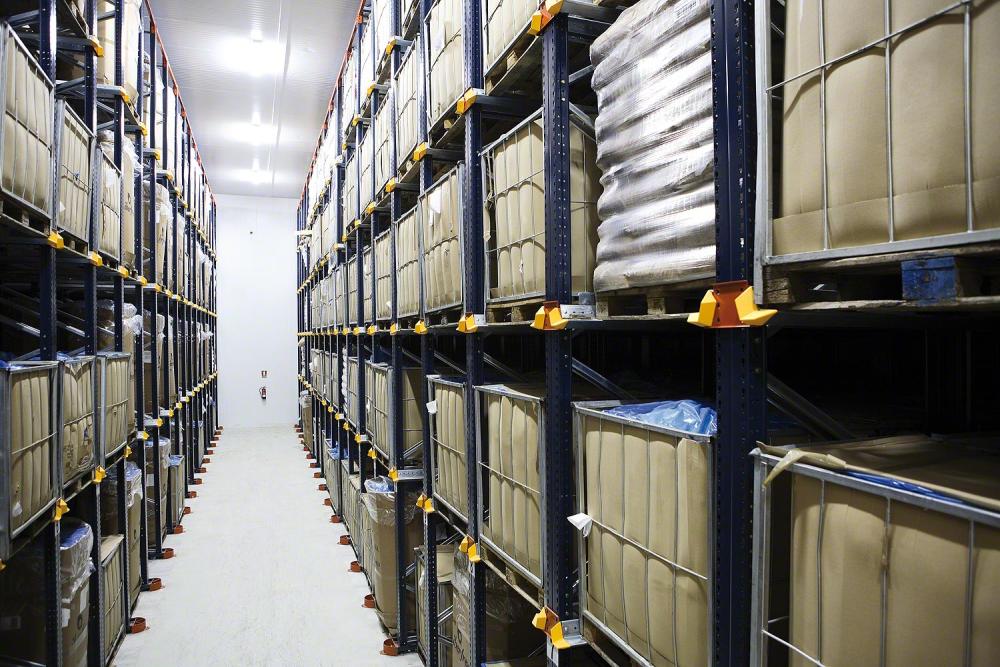
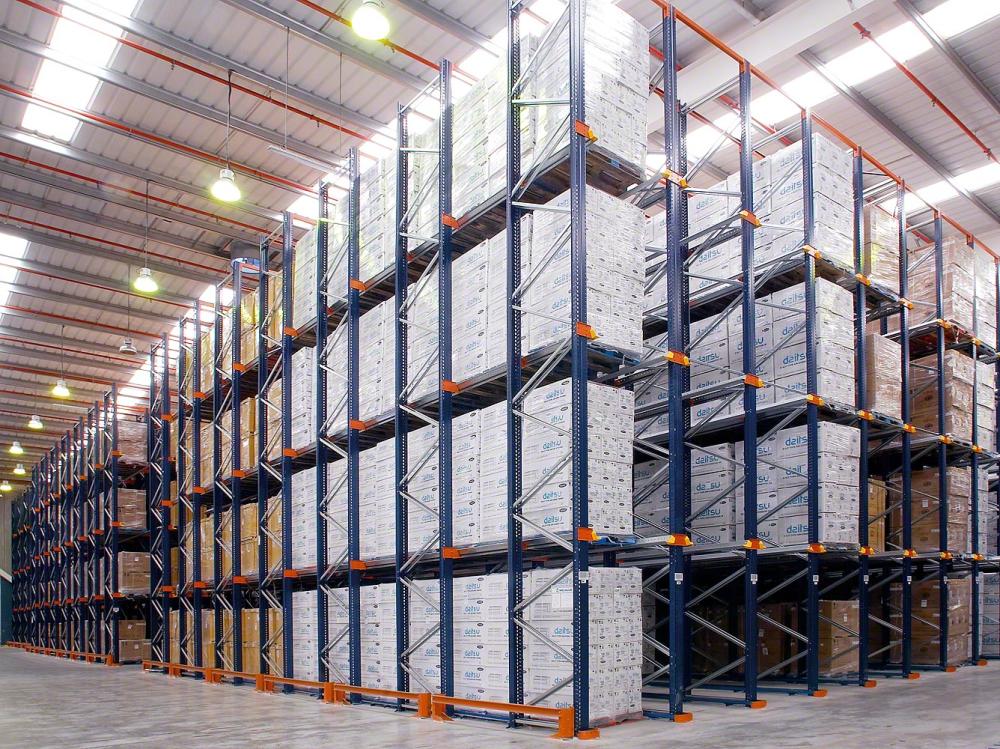
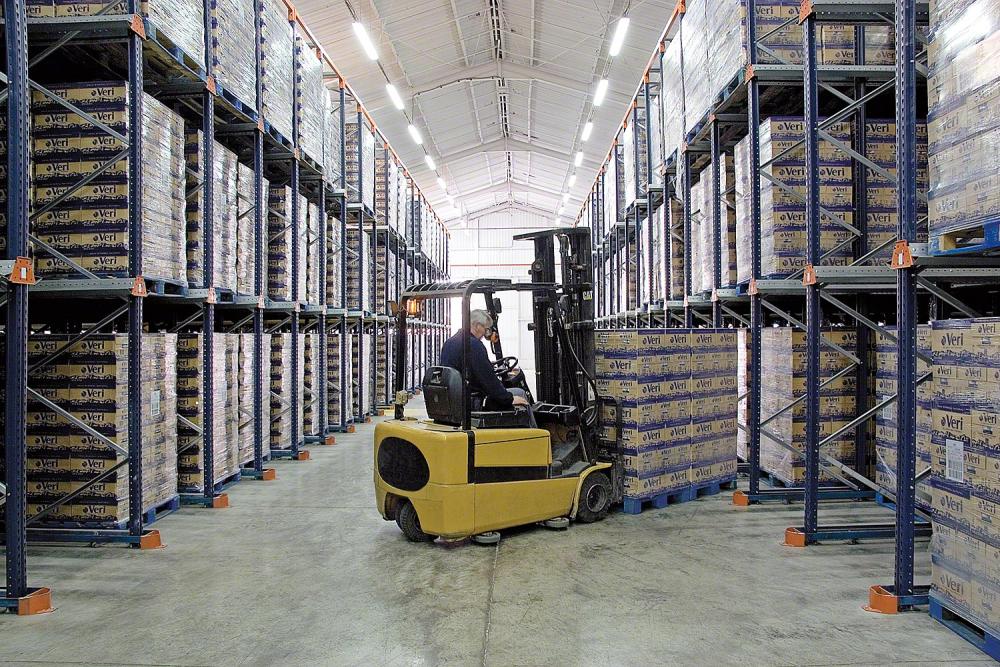
.
Schedule Your Consultation with Our Experts
W.W. Cannon’s Turnkey Service Solutions result in a strong return on your investment. Get in touch with one of our specialists today for a complimentary consultation. We’ll answer any questions you have and help you plan your next steps.